The current, editable version of this book is available in Wikibooks, the open-content textbooks collection, at
https://en.wikibooks.org/wiki/3D_Printing
History
Origins
In 1982 modern 3D Printing was devised by Dr. Hideo Kodama.[1]
In Charles Hull invented sterolithography in 1984.[2] Scott Crump would invent FDM (FFF) printing in 1989.[3]
Starting in 2004 the Open Source Rep Rap project resulted in a number of derivative commercial printers being made that were more affordable then previous offerings.[4][5]
- The first RepRap printed RepRap part in 2006.
- The first replicated RepRap printer.
- A RepRap 0.1 printing.
- A RepRap Darwin in 2007 or earlier.
Adoption
The then cheap and open source 3D printers offered by Makerbot caught the public imagination around 2010.[6][7] In 2012 Makerbot stopped open sourcing hardware and soon was acquired by Stratasys, where it would soon cease manufacturing their own printers in 2016.[8][9][10]
The 3D printer market contracted a bit in 2015.[11][12] Budget Creality printers became popular during this time.[13]
In the 2010's, both LulzBot and Prusa operated their own commercial scale printer farms to produce parts for their commercial 3D Printers.[14][15]
In 2020 during the COVID-19 pandemic, makes used tools like 3D printers to produce millions of PPE parts while supply lines were disrupted.[16][17]
- Makerbot founders with Makerbot CupCake prototype in 2009.
- A 3D printer for sale in a supermarket in 2016.
- 3D printers at a hackathon in 2016.
References
- ↑ "What You Need to Know About 3D Printing". http://ott.ua.edu/what-you-need-to-know-about-3d-printing/.
- ↑ "History of 3D Printing Makerspace". https://blogs.lawrence.edu/makerspace/history/.
- ↑ "Closing the Loop On 3D Printing". 30 November 2017. https://www.library.ucsf.edu/news/closing-the-loop-on-3d-printing/.
- ↑ "Materializing information: 3D printing and social change". https://journals.uic.edu/ojs/index.php/fm/article/download/3968/3273.
- ↑ "The Brutal Edit War Over a 3D Printer’s Wikipedia Page" (in en). https://www.vice.com/en/article/53d9vk/the-brutal-edit-war-over-a-3d-printers-wikipedia-page-reprap.
- ↑ "Making the Makerbot, A DIY 3-D Printer" (in en). https://www.popsci.com/diy/article/2010-06/making-makerbot/.
- ↑ Simonite, Tom. "Rise of the replicators". https://www.newscientist.com/article/mg20627621-200-rise-of-the-replicators/.
- ↑ Brown, Rich. "Pulling back from open source hardware, MakerBot angers some adherents" (in en). https://www.cnet.com/news/pulling-back-from-open-source-hardware-makerbot-angers-some-adherents/.
- ↑ Sharma, Rakesh. "The Real Reason Stratasys Bought MakerBot" (in en). https://www.forbes.com/sites/rakeshsharma/2013/09/24/stratasys-bold-moves-a-conversation-with-company-chairman-scott-crump/?sh=260433db1ce7.
- ↑ "The MakerBot Obituary". 28 April 2016. https://hackaday.com/2016/04/28/the-makerbot-obituary/.
- ↑ "People Aren’t Buying 3D Printers Anymore, So Companies Are Refocusing on Health" (in en). https://www.vice.com/en/article/qkv7km/people-arent-buying-3d-printers-anymore-so-companies-are-refocusing-on-health.
- ↑ "MakerBot lays off 20% of its staff—again" (in en). https://fortune.com/2015/10/08/makerbot-lays-off-20-percent-of-staff-again/.
- ↑ "Creality Ender 3 vs CR-10: The Differences" (in en). 15 July 2019. https://all3dp.com/2/creality-ender-3-vs-cr-10-3d-printer-shootout/.
- ↑ "The 3D Printers that Print 3D Printers" (in en). https://www.vice.com/en/article/539e93/the-3d-printers-that-print-3d-printers.
- ↑ "Three hundred 3D printers in one room: A quick look to our printing farm". 9 February 2018. https://blog.prusaprinters.org/a-quick-look-to-our-printing-farm_7474/.
- ↑ Commissioner, Office of the (13 November 2020). "3D Printing in FDA’s Rapid Response to COVID-19" (in en). https://www.fda.gov/emergency-preparedness-and-response/coronavirus-disease-2019-covid-19/3d-printing-fdas-rapid-response-covid-19.
- ↑ Choong, Yu Ying Clarrisa; Tan, Hong Wei; Patel, Deven C.; Choong, Wan Ting Natalie; Chen, Chun-Hsien; Low, Hong Yee; Tan, Ming Jen; Patel, Chandrakant D. et al. (September 2020). "The global rise of 3D printing during the COVID-19 pandemic" (in en). pp. 637–639. doi:10.1038/s41578-020-00234-3. https://www.nature.com/articles/s41578-020-00234-3.
Printer Types
Fused Filament Fabrication (FFF)
FFF printers operate by melting material from an extruder to produce a 3D object.
FFF printers are known for being easier to use than other printing technologies, partly due to requiring less safety equipment for operation.[1] Cartesian FFF 3D printers work by moving an extruder along an X, Y, and Z, axis.[2]
- A Prusa i3, a common cartesian FFF 3D printer. Cartesian 3D printers have a cuboid build area.
- A Fisher Delta RepRap 3D Printer. The build area on a delta printer is a cylinder with a conic top.
Stereolithography (SLA)
SLA printers use light to solidify a special liquid.[3][4]
Unlike an FFF printer, SLA printers build time is based on height and not the number of prints or object complexity, so the entire x and y build area can be used for prints with no impact on printing time.[5] Unlike FFF printers, SLA printers typically print upside down,[5] though this has little tangible effect on the final print. SLA printers can be difficult to operate.[6]
- A Formlabs Form2 SLA 3D Printer.
- Form 2 curing equipment. SLA prints require curing following the print process.
Selective laser sintering (SLS)
SLS works by fuzing powders together with a laser to create 3D objects.
Uniquely, SLS printers requires no dedicated support structures for complex geometries.[1]
- An SLS 3D Printer.
References
- 1 2 "3D Pinter Buyers Guide FFF vs SLA vs SLS" (in en). 30 August 2019. https://www.lulzbot.com/learn/tutorials/2019-3d-printer-buyers-guide-compare-technologies.
- ↑ "3D Printer Assembly Mentor2". http://www.mentor2.gatech.edu/wordpress/kit-activities/3d-printer-assembly/.
- ↑ "The Ultimate Guide to Stereolithography (SLA) 3D Printing (Updated for 2020)" (in en-us). https://formlabs.com/blog/ultimate-guide-to-stereolithography-sla-3d-printing/.
- ↑ "3D Printing: A Multitude of Machines & Materials-SLA/DLP Printing – Techbytes". https://blogs.umass.edu/Techbytes/2019/03/13/3d-printing-a-multitude-of-machines-materials-sla-dlp-printing/.
- 1 2 "How to slice 3D objects for the Original Prusa SL1 [updated with video guide"]. 19 June 2019. https://blog.prusaprinters.org/how-to-slice-3d-objects-for-the-original-prusa-sl1_30323/.
- ↑ Finnes, Tyler (1 January 2015). "High Definition 3D Printing – Comparing SLA and FDM Printing Technologies". https://openprairie.sdstate.edu/jur/vol13/iss1/3/.
Printer Specs
Introduction
You may have read about how 3D printers can do amazing things in the news, like print houses, cars, or human organs. While these things are possible, they depend on both the technology used by the 3D printer and the skill of the operator. As of 2020 most consumer 3D printers top out at printing high quality plastics at up to a quarter of a meter cubed on the high end.
With that said, there are a number of factors in a 3D printer that can make printing easier, faster, and more enjoyable. Furthermore as a technology seeing slow but steady continued advancement, capabilities of printers continue to improve over time. With the open nature of many printers, those with a deep understanding of the field can push printers beyond their expected capabilities and achieve superior results.
Enclosures & Structure
A heated enclosure can assist the printing of certain materials.[1]
Safety benefits
3D printers with enclosures typically reduce the amount of particles exposed to the operator.[2] Enclosures also help reduce the chance of accidental contact with moving or hot parts.[3]
Computer
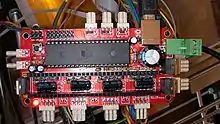
3D printers use a built in computer to precisely control internal printer operation. The board containing the computer will determine things like a printer's ability to connect to a network, expansion headers, and what firmware can be run on the printer.[4][5]
3D printer microcontrollers are typically either simple and reliable 8-bit microcontrollers, or more capable and complex 32 bit ones.[6] A more capable controller used with software that leverages it's features can allow the 3D printer to handle more of it's tasks independently of a host computer,[7] as well as potentially operate the 3D printer faster while achieving greater print quality.[8]
Drivers
Many 3D printer controller boards include built in drivers, though some use external drivers.[4] High quality drivers can improve motor operation to be more efficient and thus reduce printer noise.[9][10]
Motors
Most 3D printers use stepper motors for to move parts with percision.[11]
Rarely, servo motors are used in special 3D printers to allow feedback to control systems.[12][13] However their high cost, increased complexity, and reduced reliability makes stepper motors the typical choice for most 3D printers.[14][15]
Print head
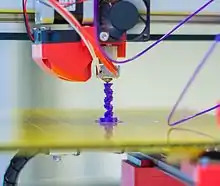
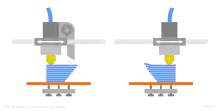
The nozzle used has an impact on print resolution.[16]
Some nozzles are made out of exotic materials like ruby to enhance their durability.[17]
Bed
Magnetic plates, flexible beds, and Bed coatings can make them easier to print with, but also require special care to keep them working well.[18][19]
Autoleveling
Some 3D printers can probe the print bed prior to printing and autolevel it.[20] This makes setup simpler, and much less tedious.
Heated Bed
A heated bed is handy for reducing part warping, a common problem when printing on an unheated bed.[21]
Filament sensor
Filament sensors are used to allow the printer to detect jams, empty filament spools, and other quality control features.[22][23]
Camera
When used with specialized software, a dedicated camera can create intriguing time lapses of prints.[24]
References
Warning: Display title "Specs of 3D printers" overrides earlier display title "Printer Types".
- ↑ "Bringing High Temperature 3D Printing To The Masses". 28 October 2020. https://hackaday.com/2020/10/28/bringing-high-temperature-3d-printing-to-the-masses/. Retrieved 6 November 2020.
- ↑ "3-D Printer Safety Environmental, Health & Safety". https://www.rit.edu/fa/grms/ehs/content/3-d-printer-safety. Retrieved 6 November 2020.
- ↑ "3D Printer Safety – Environment, Health, and Safety". https://aeroastro-ehs.mit.edu/resources/3d-printer-safety/. Retrieved 6 November 2020.
- 1 2 "32 Bit 3D Printer Board Comparison Chart". 23 January 2018. https://3daddict.com/32-bit-3d-printer-board-comparison/.
- ↑ "2020 Best 3D Printer Controller Boards" (in en). 11 October 2020. https://all3dp.com/2/3d-printer-controller-boards/.
- ↑ "A 32-bit Boost For Your 3D Printer". 10 May 2019. https://hackaday.com/2019/05/10/a-32-bit-boost-for-your-3d-printer/. Retrieved 6 November 2020.
- ↑ "Prusa Unveils New Mini 3D Printer, Shakes Up The Competition". 13 October 2019. https://hackaday.com/2019/10/13/prusa-unveils-new-mini-printer-shakes-up-the-competition/. Retrieved 6 November 2020.
- ↑ "Why Your Next 3D Printer Should Use a 32 Bit Controller". 10 January 2019. https://mechlounge.com/why-your-next-3d-printer-should-use-a-32-bit-controller/.
- ↑ Bush, Steve (11 June 2019). "TMC2209 - a part number you are going to hear more about in 3D printing (or maybe TMC5160)" (in en). https://www.electronicsweekly.com/blogs/engineer-in-wonderland/tmc2209-number-going-hear-3d-printing-2019-06/.
- ↑ "How to make your 3D printer smart and silent with the TMC2130! – Tom's 3D printing guides and reviews". https://toms3d.org/2017/12/09/tmc2130-guide/.
- ↑ "Stepper Motor Mentor2". http://www.mentor2.gatech.edu/wordpress/stepper-motor/.
- ↑ "Is It A Stepper? Or Is It A Servo?". 30 April 2016. https://hackaday.com/2016/04/30/is-it-a-stepper-or-is-it-a-servo/.
- ↑ Santos, Ramon; James, Justin; Chris, Taylor; Marshall, Stephen; Maalouf, Paul (1 June 2015). "Deltronic Solutions Delta 3D Printer". https://digitalcommons.calpoly.edu/mesp/278/.
- ↑ "Stepper Motors vs Servo Motors – re:3D Life-Sized Affordable 3D Printing". https://re3d.org/stepper-motors-vs-servo-motors/.
- ↑ Florian, David. "How to Build a 3D Printer: Stepper Motors". https://www.drdflo.com/pages/Guides/How-to-Build-a-3D-Printer/Stepper-Motor.html.
- ↑ "3D Equipment duPont-Ball Library". https://www2.stetson.edu/library/innovation-lab/3d-printers/.
- ↑ "Rubies Are A 3D Printer’s Best Friend". 30 November 2017. https://hackaday.com/2017/11/30/rubies-are-a-3d-printers-best-friend/. Retrieved 6 November 2020.
- ↑ "How to print on a powder-coated sheet". 7 June 2019. https://blog.prusaprinters.org/how-to-print-on-a-powder-coated-sheet_30178/. Retrieved 6 November 2020.
- ↑ "Improved Flexible Build Plate For SLA Is Ready To Rock". 26 October 2020. https://hackaday.com/2020/10/26/improved-flexible-build-plate-for-sla-is-ready-to-rock/. Retrieved 6 November 2020.
- ↑ "Prusa Dev Diaries #1: Mesh Bed Leveling". 20 September 2019. https://blog.prusaprinters.org/prusa-tech-insider-1-mesh-bed-leveling_30817/. Retrieved 6 November 2020.
- ↑ "Heating Up A Printrbot’s Bed". 16 June 2014. https://hackaday.com/2014/06/16/heating-up-a-printrbots-bed/. Retrieved 6 November 2020.
- ↑ "The Prusa I3 MK3S And A Tale Of Two Sensors". 8 October 2020. https://hackaday.com/2020/10/08/the-prusa-i3-mk3s-and-a-tale-of-two-sensors/. Retrieved 6 November 2020.
- ↑ "Stop Printing Air With A Filament Sensor". 4 March 2017. https://hackaday.com/2017/03/04/stop-printing-air-with-a-filament-sensor/.
- ↑ "FormerLurker/Octolapse". 5 November 2020. https://github.com/FormerLurker/Octolapse. Retrieved 6 November 2020.
Materials
_(8764959982).jpg.webp)
Plastics
FFF 3D printers typically accept a filament of a certain diameter.
Some FFF 3D printers are modified to use pellets for ease of using recycled material.[1]
PLA
PLA is a common 3D printing material. It's inexpensive and easy to use, making it a good choice as a starter material for beginners, and a general material for more advanced operators.[2]
Compared to using ABS, a typical FFF printer using PLA should emit less particles.[3]
ABS
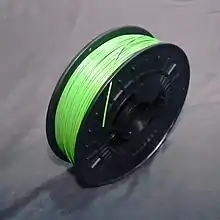
ABS is cheap and strong, but needs the right environment to print well.[4]
Compared to using PLA, a typical FFF printer using ABS should emit more particles.[3][5] Ventilation should be used when printing ABS.[4]
HIPS
HIPS is a good starting material due to its ease of use and because it is not expensive.[6]
PETG
Despite it's very different chemistry, PETG prints are similar to ABS prints but are less temperamental about the print environment making them easier to print.[2]
PETG can't be directly printed on a glass bed.[2] An intermediate material like tape must be used.[7]
Nylon
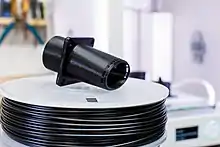
Nylon 3D prints are known for being somewhat flexible and durable.[7][8]
Nylon can also be dyed to produce different color materials.[7]
Nylon can be temperamental and difficult to work with.[4]
Flexible
Flexible filaments are expensive to buy and temperamental to use, but gives prints unique properties, allowing them to deform slightly.[2] These filaments tend to jam, and are best used on direct drive printers.[4]
Ideal Support Materials

PVA
PVA is water soluble, so PVA material melts in water while leaving the primary plastic intact.[4] This makes it ideal for support material when used in a dual extruder or a multi material printer, since supports can be dissolved instead of manually removed.
Composite Materials
Composite materials mix a printable material with a material that typically can't be printed, giving it unique properties, as well as unique challenges.
Composite Examples
Resins
SLA printers use liquid resin, instead of filaments.
Exotic Materials
3D printers geared towards directly printing in exotic materials exist.[14][15]
It is often a better idea to try 3D printing a mold in a conventional material and then using that mold to make the end product.[16][17]
3D printing food in particular has unique challenges, as the food must be printed in a way that avoids contamination and is safe to eat.[18]
- 3D printed jewelry.
- 3D printed cookies.
- A 3D Printed sugar cube.
Material Storage
When possible FFF filaments should be kept in a drybox to avoid contamination of material from humidity and dust.[21] If this is impractical, a dust filter can also be used on the filament feed.[22]
References
- ↑ "10 Tips for Converting a 3D Printer to Pellet Extrusion | Make:" (in en). 25 November 2020. https://makezine.com/2020/11/25/10-tips-for-converting-a-3d-printer-to-pellet-extrusion/.
- 1 2 3 4 "3D Printer Filaments: Definitions, Applications, and Tips". https://www.designreview.byu.edu/collections/3D%20Printer%20Filaments:%20Definitions,%20Applications,%20and%20Tips. Retrieved 6 November 2020.
- 1 2 "3D Printer Safety – Environment, Health, and Safety". https://aeroastro-ehs.mit.edu/resources/3d-printer-safety/. Retrieved 6 November 2020.
- 1 2 3 4 5 "Materials for 3D Printing – build IT @SDSU Library". https://buildit.sdsu.edu/materials-for-3d-printing/. Retrieved 6 November 2020.
- ↑ "Particles Emitted by Consumer 3D Printers Could Hurt Indoor Air Quality" (in en). https://www.news.gatech.edu/2019/10/07/particles-emitted-consumer-3d-printers-could-hurt-indoor-air-quality. Retrieved 6 November 2020.
- ↑ "Printing Materials – Innovation Studio". https://innovationstudio.mechse.illinois.edu/design-resources/3d-printable-materials/. Retrieved 6 November 2020.
- 1 2 3 "Closing the Loop On 3D Printing". 30 November 2017. https://www.library.ucsf.edu/news/closing-the-loop-on-3d-printing/.
- ↑ Meher, Robin. "Library Guides: 3D Printing at the Library of Engineering and Science: Filament Guide" (in en). https://guides.lib.purdue.edu/3dprinting/filament.
- ↑ "Magnetic Iron PLA Magnetic 3D Printer Filament" (in en). 18 September 2015. https://www.lulzbot.com/store/filament/magnetic-iron-pla. Retrieved 6 November 2020.
- ↑ "Iron-filled Metal Composite PLA". https://www.proto-pasta.com/products/magnetic-iron-pla. Retrieved 6 November 2020.
- ↑ "Conductive PLA" (in en). 18 September 2015. https://www.lulzbot.com/store/filament/conductive-pla. Retrieved 6 November 2020.
- ↑ "Color Kit" (in en-us). https://formlabs.com/store/color-kit/.
- ↑ "How Do I Dye Resin 3D Prints? - Easy To Create Custom Colored Resin". 31 January 2020. https://www.3dprintedminiature.com/how-do-i-dye-resin-3d-prints/.
- ↑ "CES 2014: 3D food printers create sweets and chocolates". 8 January 2014. https://www.bbc.com/news/technology-25647918. Retrieved 6 November 2020.
- ↑ "Engineers Create A Titanium Rib Cage Worthy Of Wolverine" (in en). https://www.npr.org/sections/health-shots/2015/09/15/440361621/engineers-create-a-titanium-rib-cage-worthy-of-wolverine. Retrieved 6 November 2020.
- ↑ Says, Jobfor778 (7 February 2020). "The beginner's guide to mold making and casting". https://blog.prusaprinters.org/the-beginners-guide-to-mold-making-and-casting_31561/. Retrieved 6 November 2020.
- ↑ "Casting Metal Parts And Silicone Molds From 3D Prints". 25 February 2018. https://hackaday.com/2018/02/25/casting-metal-parts-and-silicone-molds-from-3d-prints/. Retrieved 6 November 2020.
- ↑ "Maker Faire NY: Cocoa Press Chocolate Printer". 29 September 2018. https://hackaday.com/2018/09/29/maker-faire-ny-cocoa-press-chocolate-printer/. Retrieved 6 November 2020.
- ↑ Mishan, Ligaya (21 February 2019). "The Secret Ingredient for These Desserts: A 3-D Printer (Published 2019)". https://www.nytimes.com/2019/02/21/t-magazine/3d-printed-food-dessert.html.
- ↑ "NASA’s 3D Food Printer Will Make Pizza at Amusement Parks" (in en). https://www.vice.com/en/article/aekjnb/nasas-3d-food-printer-will-make-pizza-at-amusement-parks.
- ↑ "Filament dryboxes and alternative spool holders - not only for MMU2S". 26 July 2019. https://blog.prusaprinters.org/dryboxes-and-alternative-spool-holders-not-only-for-multimaterial-upgrade_30525/. Retrieved 6 November 2020.
- ↑ "Filament Dust Filter Helps Keep Your Print Quality High". 6 September 2020. https://hackaday.com/2020/09/06/filament-dust-filter-helps-keep-your-print-quality-high/. Retrieved 6 November 2020.
Warning: Display title "Materials" overrides earlier display title "Specs of 3D printers".
Models
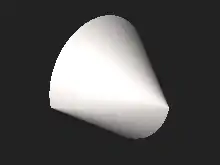
Creation
Manual
It is possible to design a 3D model from the ground up for 3D printing using standard 3D software.
3D Scanning
3D Scanning through techniques such as photogrammetry can be used to duplicate real world objects.[1]
- A 3D Scanner that photographs objects as they move on a turntable.
- A less common but quicker scanner type uses a chamber filled with cameras that surround the subject.
Editing
Some models, such as those created by 3D scanning, require cleanup before they can be printed.[2]
3D models on a computer can represent things that are impossible to recreate in reality. Thus for a model to be 3D printable, it must represent an actual object, without errors in an object that would cause the interior of the model to not be watertight.[3]
File Formats
STL

.stl has become a defacto standard for many 3D printer slicer programs.[4][5]
3MF
3MF is an open source format that offers a number of improvements over .stl, such as being more error resistant and including color information.[6][7]
Related Wikibooks
References
Warning: Display title "Models for 3D printing" overrides earlier display title "Materials".
- ↑ "Photogrammetry 2 - 3D Scanning simpler, better than ever!". 3 December 2018. https://blog.prusaprinters.org/photogrammetry-2-3d-scanning-simpler-better-than-ever_29393/. Retrieved 6 November 2020.
- ↑ Hoya, Billy. "LSC-North Harris Library Research Guides: Creating 3D Objects using Photogrammetry: Step 3: Viewing, Printing, and Editing" (in en). https://nhresearch.lonestar.edu/c.php?g=1030154&p=7466325.
- ↑ Charlesworth, Sean (19 March 2014). "Bits to Atoms: 3D Modeling Best Practices for 3D Printing". https://guides.hshsl.umaryland.edu/c.php?g=163717&p=1075332.
- ↑ Mellinger, Margaret. "LibGuides: 3D printing : 3D Printing Tips" (in en). https://guides.library.oregonstate.edu/3Dprinting/3dprinting_tips.
- ↑ "Art + Design - Tutorial - Preparing 3D Print Files for the Zortrax Printers". https://art.illinois.edu/index.php/tutorial-preparing-3d-print-files-for-the-zortrax-printers.
- ↑ "3MF File Format (3D Printing) – Simply Explained" (in en). 8 October 2018. https://all3dp.com/2/3mf-file-format-3d-printing-simply-explained/.
- ↑ "3MF file format and why it’s great". 1 November 2019. https://blog.prusaprinters.org/3mf-file-format-and-why-its-great_30986/.
Slicing Software

Slicers
A slicer converts a 3D model of an object into layers that a 3D printer can understand.
Many slicers include convenience features. A common example includes printer and material presets.[1] Some FFF slicers include uncommon features that help with complex geometry and print reliability.[2]
SLA slicers produce different support structures then FFF slicers.[3]
Infill
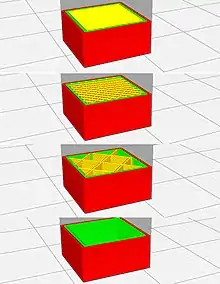
Infill determines the amount of material on the inside of a print.
A number of creative infill patterns can be used for different purposes, such as 3D infills[4] and gradient infills.[5]
GCode
Many 3D printers use GCode for instructions on operation. However not all generated GCode is the same.
There are a number of software packages oriented around GCode. Some software analyses GCode and provides helpful information about a print.[6] GCode post processors can improve print speed and quality.[7] Non-planar GCode can also improve 3D printing results.[8][9]
Slicer features

Layer Height
Some slicers support variable layer height, allowing for the printer to slow down on detail heavy areas for better quality, and speed up printing for less detailed areas.[10]
Pausing
Some slicers allow prints to be paused to allow operators to swap materials partway through, or to add things like magnets to the internals of the print.[10][11]
References
Warning: Display title "Slicing Software" overrides earlier display title "Models for 3D printing".
- ↑ "PrusaSlicer - Prusa3d.com - 3D printers by Josef Prusa". https://www.prusa3d.com/prusaslicer/.
- ↑ "Pathio: New 3D Slicer From E3D". 24 February 2019. https://hackaday.com/2019/02/24/pathio-new-3d-slicer-from-e3d/.
- ↑ "How to slice 3D objects for the Original Prusa SL1 [updated with video guide"]. 19 June 2019. https://blog.prusaprinters.org/how-to-slice-3d-objects-for-the-original-prusa-sl1_30323/. Retrieved 6 November 2020.
- ↑ "3D Internal Structure For Better 3D Printed Objects". 10 June 2016. https://hackaday.com/2016/06/10/3d-internal-structure-for-better-3d-printed-objects/. Retrieved 6 November 2020.
- ↑ "Gradient Infill Puts More Plastic Where You Want It". 21 January 2020. https://hackaday.com/2020/01/20/gradient-infill-puts-more-plastic-where-you-want-it/. Retrieved 6 November 2020.
- ↑ "GCode Analyzer/Visualizer by hudbrog" (in en). https://www.thingiverse.com/thing:35248. Retrieved 6 November 2020.
- ↑ "This GCode Post-Processor Squeezes Lines Into Arcs". 3 November 2020. https://hackaday.com/2020/11/03/this-gcode-post-processor-squeezes-lines-into-arcs/. Retrieved 6 November 2020.
- ↑ "3D Printering: Non-Planar Layer FDM". 27 July 2016. https://hackaday.com/2016/07/27/3d-printering-non-planar-layer-fdm/. Retrieved 6 November 2020.
- ↑ "makertum/non-planar-layer-fdm". 6 November 2020. https://github.com/makertum/non-planar-layer-fdm. Retrieved 6 November 2020.
- 1 2 "PrusaSlicer 2.2.0 is out! Hollowing, support for 3rd party printers and more!". 25 March 2020. https://blog.prusaprinters.org/prusaslicer-2-2-0-is-out-hollowing-support-for-3rd-party-printers-and-more_32728/. Retrieved 6 November 2020.
- ↑ "Change Filament At Z Cura Plugin by rawlogic" (in en). https://www.thingiverse.com/thing:2077884. Retrieved 6 November 2020.
Color Printing
Methods of 3D printing in color
One way to achieve color 3D printing is to use a multimaterial printer.[1] This requires loading different color materials into the printer, as well as setting up the model(s) and printer software correctly.
One solution to color FFF 3D prints is to simply place markers along the feed of a white filament.[2]
Failing anything, color can be added in post processing steps, such as by painting the print.
Gallery
- A multicolor print made on a FFF printer.
- A multicolor print made by a printer designed to print in color.
- A MultiMaterial upgrade for Prusa printers.
- A color sandstone 3D print.
References
- ↑ "3DP – Carnegie Center". https://carnegie.jhu.edu/3d-printing/.
- ↑ "Sharpie Mount Brings Some Color To Your 3D Prints". 2 November 2020. https://hackaday.com/2020/11/01/sharpie-mount-brings-some-color-to-your-3d-prints/. Retrieved 6 November 2020.
Warning: Display title "Color Printing" overrides earlier display title "Slicing Software".
Post Processing
General Post Porcessing Techniques
Sanding is commonly used on 3D prints to smooth prints or remove small imperfections.[1]
Acrylic paint, model paint, nail polish, markers, and spray paint are common ways to add color to a print.[2][3]
Salt annealing and plaster annealing can give parts a unique finish, and alter strength properties of a print.[4][5] Annealing techniques may be effective to improve prints with slight warping.[6]
.jpg.webp)
Process Specific Techniques
Post Processing is mandatory for most SLA prints, as extra resin must be removed and desired resin must be hardened.[7][8]
Prints made with ABS plastic can be smoothed with careful application of an acetone vapor.
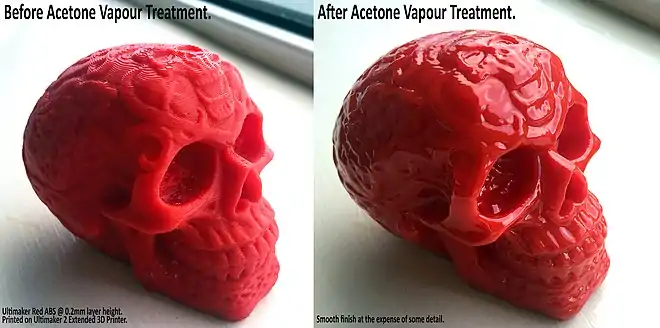
References
- ↑ "Mansfield Library" (in en). https://www.lib.umt.edu/tech-spaces/pawprint/3d.php.
- ↑ Jalal, Rita. "Coloring 3D Printed Objects – build IT @SDSU Library". https://buildit.sdsu.edu/coloring-3d-printed-objects/.
- ↑ "3D Print Customization Florida State University Libraries". https://www.lib.fsu.edu/3d/print-customization.
- ↑ "Take This 3D-Print Post-Processing Method With A Grain Of Salt". 27 October 2020. https://hackaday.com/2020/10/27/take-this-3d-print-post-processing-method-with-a-grain-of-salt/. Retrieved 6 November 2020.
- ↑ "Plaster Annealing 3D Prints For Strength". 24 September 2020. https://hackaday.com/2020/09/24/plaster-annealing-3d-prints-for-strength/. Retrieved 6 November 2020.
- ↑ "Final Update: FFF Strength Optimization". 2165. https://additive-mfg.me.wisc.edu/?p=2165.
- ↑ "3D Printering: Wash Parts Better And Make Solvent Last Longer". 6 October 2020. https://hackaday.com/2020/10/06/3d-printering-wash-parts-better-and-make-solvent-last-longer/. Retrieved 6 November 2020.
- ↑ "customer_v2". https://support.formlabs.com/s/article/Form-2-Basic-Finishing-Steps?language=en_US. Retrieved 6 November 2020.
Warning: Display title "Post Processing" overrides earlier display title "Color Printing".
Maintenance
Introduction
3D printers are complex machines that require maintenance to operate efficiently.
Diagrams






References
Warning: Display title "Maintenance of 3D printers" overrides earlier display title "Post Processing".
Applications
Rapid Prototyping
When making prototypes, having quick tangible feedback is of great importance for spotting facets of a work which are not immediately clear on paper or in computer models.
One off production
When producing just one or a few items, the inherent inefficiencies of 3D printing matter much less, especially if the properties of 3D printed materials are adequate or if the time to begin production is limited (Taking just a few hours or days assuming the model is ready).
Accessibility
3D printing can be used to create tactile versions of visual media like artwork or maps for the blind.[1][2]
Logistic stopgap
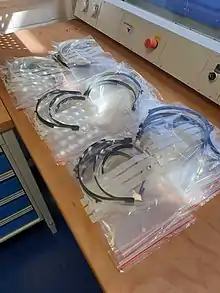
When supply chains are disrupted in an emergency, local 3D printer owners are able to produce low quantities of vital materials and parts, ensuring a constant, if very small stream of new supplies, while logistical challenges are fixed. This very scenario was seen in the early days of the COVID-19 pandemic, when 3D printer operators made PPE and ventilator parts for hospital staff.[3][4] It is also a strategy employed by some disaster preparedness strategies.[5]
References
Warning: Display title "Applications of 3D printing" overrides earlier display title "Maintenance of 3D printers".
- ↑ "Please Touch the Art: 3D Printed Masterworks for the Blind" (in en). https://www.vice.com/en/article/4xqbnw/please-touch-the-art-3d-printed-masterworks-for-the-blind.
- ↑ Karbowski, Caroline (24 February 2020). "See3D: 3D Printing for People Who Are Blind". doi:10.14448/jsesd.12.0006. https://scholarworks.rit.edu/jsesd/vol23/iss1/6/.
- ↑ "One Way to Help Strapped Hospitals? Print PPE Using 3D Printers" (in en). https://www.npr.org/2020/03/28/822911643/one-way-to-help-strapped-hospitals-print-ppe-using-3d-printers. Retrieved 7 November 2020.
- ↑ Fracassi, Cristian; Romaioli, Alessandro (22 March 2020). "Opinion We Made Copies of Ventilator Parts to Help Hospitals Fight Coronavirus". https://www.nytimes.com/2020/03/22/opinion/ventilators-coronavirus-italy.html.
- ↑ "Doomsday Preppers Are Planning to 3D Print Their Way Through the Apocalypse" (in en). https://www.vice.com/en/article/9a3q75/doomsday-preppers-are-planning-to-3d-print-their-way-through-the-apocalypse.
Development
Progress
- Minimum Viable Product achieved on November 29th, 2020.
Pages in Development