In Section 2.1 we described combining multiple ideas to form self-improving systems, and starting points for them called seed factories. The concept of a seed factory is fairly new. So in this section we review how it evolved, the current state of the concept, what is still unknown about it, and further research to address these unknowns.
1.0 - Seed Factory Concept Evolution
The seed factory concept evolved to its present state since the late 20th century, after the necessary precursor technologies and ideas were developed. They include tools from the simplest hand ones to modern complex machines, and power sources starting with human muscles to the wide variety we use today. Self-controlled machines can now operate with less labor needed. Coupled with non-human power sources, people began to imagine them copying themselves like living things. Autonomous replication is quite complex, so human-assisted growth and evolution was an added idea. This enables design to be done in smaller steps rather than all at once. Methods from systems engineering and software development can then be used in this step-wise approach.
Human societies have had complex systems for a long time. What is new is using our accumulated knowledge and experience to intentionally design systems for self-improvement from a starting point. Production systems that can self-expand, upgrade, and replicate enables exponential growth. This provides a physical base to address large-scale problems. Our store of knowledge is not fixed, and system evolution is open-ended. So these kinds of systems do not reach a final end-point. We can expect them to continue to grow and evolve, so long as people are willing to put in the effort to do so.
The following headings cover development of the relevant ideas in more detail.
1.1 - Automation
Ancient tools like the hand axe have no moving parts and are powered by human muscles. They have existed longer than modern humans. Machines have moving parts such as gears. Most of the elements making up machines were invented after agriculture began about 12,000 years ago. The use of animal muscles for additional power also developed after their domestication. These times are short relative to the 300,000 year age of our species. Windmills and water wheels to power machines only started about 2000 years ago. Controlled fire is ancient, but driving machines with it is only a few centuries old. The complexity of our machines, and new power sources for them, has only accelerated since then.
Animals have some degree of self-control. For example, a horse-drawn cart may continue at a steady pace following a winding path without constant attention from a human driver. Their senses and nervous system control their muscles to do this. The earliest mechanical controls were to keep clocks running at a steady pace. One for a water clock was described about 270 BC. Such controls work by sensing something about the device, then applying an adjustment to reach the desired condition. This "feeding back" from the current state to get to the desired state is known as Feedback Control. More complex machines driven by wind, water, or fire increased the need for control devices to keep their speed, pressure, and temperature within safe and desired limits. Such control devices were invented starting in the 17th century and came into widespread use with the Industrial Revolution in the 18th century.
Electric power delivery was introduced in 1882, prompting rapid development of on-off type controls in the early 20th century. Humans were still making the control decisions based on instrument readings. In the 1930's the control devices started to use graduated responses in addition to on-off. Instruments also started to produce an electrical rather than visual signal. This allowed the control devices to calculate the response directly, without involving humans.
Electronic Devices modulate the flow of electrons or Current. This enables carrying information in addition to delivering power. Various types of active devices were developed since the start of the 20th century. They change informative signals in more complex ways, such as varying the output signal based on one or more input signals. Such devices have been connected in ever-increasing numbers to create circuits that perform more complex functions. In the mid-20th century solid-state electronics were introduced, which dramatically shrank circuit sizes.
Electrical and electronic controls have enabled individual machine functions, entire complex machines, and multiple machines comprising a process or factory to operate with less of our labor. They control themselves, rather than needing people to make decisions. This technology is called Automation. It developed rapidly through the 20th century, accelerating since the middle of the century with the development of Computers. These use complex electronic circuits to carry out sequences of arithmetic or logical operations, based on stored programs and data. The stored information can change, making computers very flexible. When used to control machines their tasks can also change, rather doing the same things multiple times. As of 2020, computers and automation are still rapidly evolving.
1.2 - Replication
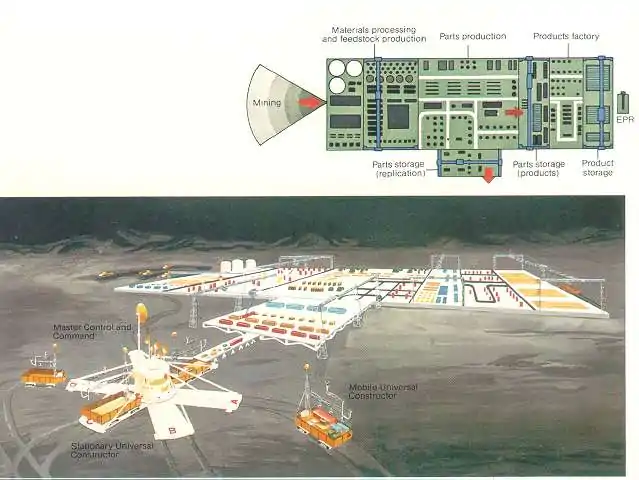
Growth and reproduction has been observed in nature for as long as humans have been around. But it was not until the mid-20th century that it was proposed machines could also do these things. In manufacturing we often use various tools and machines to make identical copies of a product. The product copying itself is a recent idea known as Machine Replication, or Self-Replicating Machines. This is a collection of machines or factories that can make an identical copy of itself. The idea of machine replication became evident as soon as control theory and automation were well-enough developed. It got serious theoretical study in the same mid-20th century period, starting with work on Reproducing Cellular Automata by John Von Neumann. A 2004 book by Freitas and Merkle, Kinematic Self-Replicating Machines thoroughly reviews the literature for replicating systems to that point.
A 1982 NASA report, Advanced Automation for Space Missions (AASM), introduced the concept of a replicating factory for use on the Moon (Figure 2.1). Their approach was to copy the original factory hardware multiple times, using local materials and energy. Once enough copies had been made, the combined production capacity would turn to making an unspecified end product to support NASA goals. The AASM study introduced the term Seed Factory to mean the first unit of the factory delivered from Earth to the Moon. In these books we use it for the more general concept of a starter set which can expand by multiple methods besides directly copying its own parts.
Communications bandwidth from Earth at that time was too low for remote control. The AASM concept therefore assumed the factory would be fully automated. The estimated computer power for this was 2 GB memory and 35 GB storage, far beyond what was available at the time of the study (1980). The complete seed factory was also estimated to be 100 tons in mass. The Apollo Lunar Module could deliver about 5 tons, requiring many flights, and it had been retired by 1980. So there wasn't any practical way to deliver the factory. Lastly, there was no pressing need for mining and production on the Moon. So for all these reasons the concept was not developed further.
The study did consider availability of raw materials and material processing methods, but did not do a full resource flow accounting of all materials, energy, and data. The first spreadsheet program, VisiCalc, had just been introduced in 1979, and Computer Simulation and Numerical Analysis Software were at a relatively early stage of development. The tools at that time could not have handled such a complex design. The study also neglected to consider Earth applications of the idea, because NASA's goals do not include improving manufacturing on Earth. Despite these shortcomings, the AASM study is probably still the best attempt to date of describing a fully replicating factory.
1.3 - Updating the Seed Factory Concept
Making several changes to the 1982 replicating factory concept greatly simplifies building useful, functioning systems. The first is allowing people to help the machines. Humans can do many general-purpose tasks, and replicate ourselves and our knowledge. Second is allowing a set of people and their equipment to make less than all the parts needed for a full copy. The remainder are supplied from elsewhere. Third is changing from only copying existing parts and materials to making new and different ones. These are assembled into new equipment not in the original set.
New items are added to the set recursively. Each new tool or machine is used along with previous ones to make the next in the series. More people are added as needed to run everything. This process continues until either the expanded set can make all the products desired, or can make a copy of the original set. In the second case, some of the people can then work only with the copy of the starter set. At that point the system has fully copied itself. This path of replication by way of intermediate steps is called Indirect Replication, where the original AASM approach was direct replication using only the seed factory.
The AASM study assumed the seed factory did nothing but copy itself until some desired capacity was reached, then change to making an unspecified space project. So our last change is using part of the factory output earlier to make products for sale or trade. This helps pay for outside supplies of materials and parts that can't be made internally. Where the 1982 concept was on the Moon, isolated from the rest of civilization and replicating on its own, our changes to the concept integrates the system with the rest of society.
These changes lead to the updated seed factory concept as we describe it in these volumes. However, making copies of starter sets isn't the final purpose of a factory. Rather, it is a means to an end - making the things people need and want. So self-expansion by making new equipment and selling products to pay for new equipment is altered at some point. A Mature Factory includes equipment to make finished items for people to use, rather than more expansion itself. The set of equipment in the mature factory will depend on the purposes and goals of the people who design and build it. Making products to use, rather than improving the factory, can begin right from the start or at some later time. The proportions can change as needed. A conventional factory is then one that makes only useful products from the start, and does not make anything to improve itself.
The next few headings provide additional details on the changes from the 1982 concept. We don't yet know if a mature factory can copy itself the way the 1982 study assumed - unassisted by people and outside supplies. That is a topic for further research discussed below. There is also more work needed to find the best starter sets to reach a given mature state, and how seed factories should be funded, organized, and operated.
1.4 - Diversification, Flexibility, and Growth
The AASM study assumed full replication of a starter factory. It did not consider starting with a simpler subset and adding new equipment over time. Requiring full replication from the start makes the initial hardware both more complicated to design, and physically larger. Even if you are theoretically able to replicate 100% of your equipment, from an engineering standpoint it might not make sense. It is likely that a given location will not have all the needed materials in usable amounts. A 1986 study of building solar power satellites found 98% of the materials could be sourced from the Moon, but the other 2% needed to come from Earth. It is also likely that some parts, like computer chips, are difficult to make within a small factory, compared to simply buying them. Due to these materials and difficulty problems, a practical design will most likely copy less than 100% of its parts. These problems are likely to be true for any location, not just the Moon. With some materials and parts being imported in an practical design, it is a small conceptual step to also allow the percentage of outside supplies to vary with time.
A starter set can then begin by making some fraction of the parts and materials internally, with the remainder supplied from elsewhere. The internal plus outside sources are used to build new equipment. The added equipment enables making a wider range of items internally. This recursive self-upgrade is done as many times as needed. We call this process of adding more equipment to widen the product range Diversification. It can continue until you make the full range of desired products, or reach the full set of equipment which is practical to use. We call a factory that reaches these full capacities Mature.
One category of new equipment is extensions or attachments for existing equipment. For example, extension rails and a larger table allows a CNC mill to make larger parts. Conventional farm tractors are examples of machines that have a multitude of different attachments. A modular vehicle chassis or a robot arm in a factory can similarly accept a range of attachments. Items like assembly jigs, holding fixtures, molds, and custom cutting bits can make a basic machine more flexible. One criterion for choosing a member of the starter set is then how many of these added items you can use with it, and thus how many different tasks it potentially can do. We call this feature Flexibility. The more flexible the starter machines are, the fewer of them you need to get started.
A conventional factory starts with a full set of needed equipment. A seed factory starts with a smaller set of equipment, plus a set of design information for the rest. Modern computers can store this information at very low cost. So the seed factory plus expansion plans will be cheaper as a starting point, but may take longer to grow to the same output level. Conventional factories are designed to make a specific range of products. A mature self-upgraded factory can make much of its own equipment in addition to these specific products. It is therefore more capable by having a wider range of possible products.
It is not necessary to stop the self-upgrade process once a specific range of products can be made. Neither is it necessary to stop once "Practical Replication" is achieved. That is copying all its own parts which are practical to make at a given location. Additional equipment can be added beyond those points for other processes, materials, and products. Self-improvement can continue until resources and equipment space are limited at a location, or people run out of things they want to make. So seed factories have more growth potential than a conventional factory.
1.5 - Scaling
A simplified starter set is one way to reduce the complexity and cost of getting started. Scaling of equipment sizes is another approach. The AASM study only considered making exact copies of the seed factory, but we know that equipment comes in various sizes. It should be evident that tools and machines of a given size can be used to build larger products. Otherwise our civilization could not build things like skyscrapers and giant cargo ships. One way to make larger items is by assembling them from smaller parts, using fastening methods like welding or bolting. So one generation of tools and machines can be used to make larger (or smaller) versions in the next generation. Scaling of accuracy, rather than size, can be used to make progressively more accurate versions of equipment types.
Another scaling method is to use processes which are open-ended in at least one axis. An example is a rolling mill to make structural steel shapes. The rolling process does not limit the length of the metal parts you feed through it. It is only limited by how much room you have on either side. An example in two and three dimensions is casting of concrete structures. The forms, mixing, and pouring equipment can be mobile, working on different parts in series. So a finished structure like an airport runway can be many times larger than the equipment that made it.
Scaling can start with whatever size is most convenient, then applied multiple times in successive equipment generations, until you reach a desired final size. In theory you could start with microscopic machines for minimum size, cost, and materials used. In practice whatever operations and maintenance are not yet automated require human interaction. These tasks should start out at a scale people can work with directly. Otherwise you need additional equipment to handle very small or very large tasks.
Each generation of scaling requires more time, and may leave behind equipment in sizes not needed later. Scaling also requires some redesign for each generation, since not all parts of a system scale equally. Finally, the design effort for a given number of machines in a factory is relatively constant no matter what size they are. So the savings in materials from starting smaller will eventually become negligible relative to the total design cost. All these factors go into choosing what size to start with, and how to scale afterwards.
1.6 - Technology Level
The final assumption made by the AASM study was full automation. This was because remote control was not possible with 1980 communications technology for even one factory on the Moon, let alone 1000 copies. We don't need to make that assumption for the current seed factory concept. For one thing, certain tasks are either too hard to automate, or are done so rarely it is not worth trying to automate them. It is easier for people to do those things. For another, trying to automate everything at the start requires more equipment and more design work. Lastly, modern communications has improved enough that remote control is quite possible over long distances.
Instead of assuming full automation, you start with whatever is practical. CNC machine tools and 3D printers are existing types of automated equipment. So they are good candidates for a starter set. Over time you can add robots and automated inventory systems to increase automation in a factory. Since by design you can partly make your own equipment, adding them later will be less expensive than trying to buy them all at the start. Starting with partial automation also allows you to defer design of the more complex automation until later. This lowers the cost to get started.
The lowest possible cost is starting with no tools whatsoever, and bootstrap by making crude tools by hand. But with modern civilization, this isn't necessary. For most projects it makes sense to start with an affordable amount of hand and power tools, some larger stationary and mobile machines, and some smart tools that use automation, robotics, software, and AI. Buying some of these already-designed and in-production items will be worth the time and labor savings over starting from scratch. The exact amount and what kinds of equipment to start with will depend on the people involved, available resources, location, and goals for the project.
1.7 - On Starter Sets and Upgrades
Starter sets are not a new idea. They were used throughout history, especially when settling new areas. At first, these were hand-carried tools used to hunt, chop, and grind. The need to carry them limited their total mass. With more advanced technology, ships and land vehicles could carry larger starter sets, and then structures set up at the destination to house them. These included plant seeds, animals, tools, and an inventory of finished items like nails and cloth that could not be made immediately.
Once settlers arrived they set about clearing, planting, and building. Over time they started making their own tools and products. Until then, they traded with other locations for items they could not yet make. The contents of a starter set has varied over time, but it was commonly understood that you needed one to live in a new location. In the modern world, the idea of starting fresh at a new location has become less common. Improved transportation and cheap mass production can deliver enough finished items and supplies at reasonable cost. But an idea can still be useful, even if it is not currently popular. We can update the basic idea of a starter set by using 21st century equipment and methods. We can then use it in already settled areas to start new projects at lower cost. It can also be used in more difficult and remote locations that would otherwise be too hard to use.
People who have workshops are used to making storage, workbenches, jigs, and other upgrades with the tools and machines they already have. So the idea of self-improvement is already part of their thinking. Sometimes wood and metal shops will build complete new machines using equipment they already have. But such workshops typically don't produce all of the component parts. They make the easier items, and buy parts like bearings and motors which are harder to make.
[Merge]People have copied tools using other tools throughout history. For example, a woodworker can use an existing workbench to make another workbench. But it is the person doing the copying, not the tools copying themselves. Some projects where partial self-expansion and replication are involved, or research towards such systems include:
2.0 - Current Status and Projects
So far as we know, no one has yet designed and operated a workshop or factory that combines intentionally using a starter set, making most or all of the items for its own expansion, and using high levels of automation. Besides agriculture and some software, neither has full self-replication of system elements been reached. A hybrid system like a farm has both biological and non-living elements. The plants and animals, including the farmers, can self-replicate, but not copy the buildings and equipment except at a very low technical level.
What work has been done on artificial self-replication is largely theoretical, with a limited amount of simple prototypes. So these methods are not as well developed as other kinds of manufacturing - who have had multiple projects built, operated, and have accumulated knowledge and experience on how. We would like to bring self-improving systems and seed factories (SIS & SF) to a similar level. So this heading will look at what has been done so far, and in 3.0 lay out open questions and further work needed.
New ideas and methods, like the ones we describe in these books, do not develop in isolation. They make use of knowledge and experience in other fields of science, technology, and the social sciences. So it is also necessary to understand the current status and progress in these other areas. A detailed discussion here would both be unreasonably long and become rapidly out of date. Instead, we will point to other resources for this information. As work on SIS & SF makes progress, we would expect to regularly update information from other fields, and incorporate it as needed.
2.1 - Existing Knowledge and Experience
We want to design projects which can evolve from a starter set to highly integrated and self-operating systems. They both make many improvements for themselves, and a variety of finished products for others. To be efficient, we expect they will use a lot of computers, software, and communications in running them. We also expect to use automation, robotics, and artificial intelligence to minimize human labor. Collectively these technologies enable Smart Tools and Smart Systems which can mostly function on their own. Information technology and smart tools are then core subjects for the evolution of these types of projects. Both subjects are making rapid progress, so keeping up-to-date will be very important. Starter sets and more basic projects can rely on simpler equipment, without extensive IT and smart features. Such equipment is not evolving as quickly, so it needs less attention to stay current.
Information Technology
Computers, software, and telecommunications are collectively called Information Technology (IT). IT equipment is used to store, retrieve, transmit and manipulate data. Such equipment is used in all stages of modern manufacturing, from initial design of the production equipment and products, to control of the factory operation, and for communication with outside entities. It is a very large industry, with estimated spending of $3.5 trillion in 2017, or 4.5% of the world's US $77.8 trillion of measured economic activity (Gross World Product). Amazon's website lists over 90,000 book results when searching for "information technology", and the Library of Congress returns the maximum of 10,000 results for that term. More recent books from both sources are a starting point to understanding the state of this field.
Probably the most significant aspect of IT is the rapid improvement in hardware and software elements that make up IT systems. For example, when self-reproducing factories were studied by NASA in 1980, the estimated computing power to run them was equivalent to the fastest supercomputer in the world. Today, that same computing power is available in a smartphone or tablet, and continued improvement is expected. The articles and subcategories listed in Wikipedia's Information Technology category can be used as a starting point for more specific subject areas. There are also numerous IT Organizations whose members and publications are sources for current information.
Smart Tools and Systems
These replace some part of human decision-making with hardware and software to control equipment. It includes the fields of automation, robotics, software, and artificial intelligence. The following Wikipedia articles and those they link to can serve as starting points for their current status: Automation is the use of control systems and information technologies to reduce the need for human work in the production of goods and services. Robotics is concerned with programmable machines, as distinct from machines that perform a fixed set of operations. The two fields are closely related and have developed in parallel since the mid-20th century, when electronics and sensors reached a sufficient level of development. Software is a collection of computer programs and related data that tells a computer what to do. The computer in turn can control tools and machines. Artificial Intelligence in general refers to machines which mimic the functions of the human mind. For the purpose of our work, we are concerned with functions used in making goods and services.
The field of automation is large enough that the International Society of Automation has over 40,000 members, and the Library of Congress lists nearly 900 titles when searching "Manufacturing Automation". Of particular interest is Numerical Control of Machine Tools, known as NC or CNC (Computer Numerical Control). Machine tools shape parts from metal or other rigid materials from unshaped stock materials. Since machine tools are themselves mostly made of metal parts, then such tools can be used to make more of themselves. Also of interest is 3D Printing, which makes parts by adding material under computer control. These printers can make some of their own parts, to the extent they are made of the same kind of materials they can print. Both machine tools and 3D printers also can make parts for many other kinds of machines, and for many finished products.
The field of robotics has rapidly grown since the mid-20th century, when the term "robotics" was coined and the first modern programmable robot developed. There are now a number of Organizations and Companies involved, and the IEEE Robotics & Automation Society has over 13,000 members in 120 countries. Amazon's website lists over 20,000 books related to robotics, and the Library of Congress lists over 4600 items for the search term "Robotics".
The fields of Computer Science and Software Engineering have also developed since the mid-20th century, in parallel with the development of electronic Computers. The number of software developers world-wide is now in the tens of millions, and computers and software make up essential elements of our civilization. They will likewise be essential in the more advanced versions seed factories and self-expanding systems.
The AI field was founded in the mid-20th century, but progress was slow in the 1970's to 1990's (the AI "Winter") due to difficulties with practical applications and available computing power. Since then theoretical, cross-discipline, and hardware improvements have led to rapid progress in the field. The Association for the Advancement of Artificial Intelligence now has over 4,000 members, and Amazon lists about 30,000 titles about AI & Machine Learning. The Library of Congress catalogs nearly 10,000 items under the terms "Artificial Intelligence" and "Machine Learning".
Other Fields
In addition to the core subjects mentioned above, there are many other branches of science, technology, and the social sciences which will be useful in designing and building self-expanding and self-improving systems. Among the sciences are Geology, Chemistry, and Agricultural Science, for understanding of raw materials, processing them, and growing biological products. Among the technology fields are Construction, Mechanical, Electrical, Transportation, Mining, and Manufacturing Engineering. Social Science is concerned with people as individuals and how they interact in groups. It is relevant to any projects that have people included. These areas of knowledge are not the only ones that may prove useful.
Science and technology together are enormously broad subjects. When working on SIS/SF type projects, you can start to identify which parts are relevant using Wikipedia's outlines of the Natural and Physical Sciences and Technology and Applied Sciences, and the many individual articles and references linked from them. Another starting point is the Library of Congress' Subject Classification Outlines, particularly classes Q, S, and T. From those outlines you can identify more specific subjects, and then specific titles using the Library's online catalog. Beyond online and published information, it is very useful to contact individuals working in the particular fields, and get their help identifying the current state-of-the-art.
2.2 - Related Projects and Technology
The previous heading identified broad fields of knowledge that are relevant to self-improving and seed factory type systems. They can also be used for any project or product such systems can in turn produce. A subset of these fields, and activities that use them, are more closely related to the subjects in these books. The Seed Factory Project in particular is entirely devoted to it. This list of related work is not yet complete:
Related Subjects
- An entire civilization, including the people in it, may be considered self-expanding and have self-replicating elements. Thus the growth and evolution of civilizations and their technology is of interest.
- Genetically engineered organisms which can replicate have been produced, so biotechnology is a related field.
- Software systems are capable of copying themselves, given suitable supporting hardware, so much of computer science and software engineering is relevant.
Existing Automation and Robotics
- There are a large number of factories which use some level of automation. Some of these make the same type of product they use in the factory themselves. A notable example is Haas Automation, the largest machine tool builder in the western world. Two thirds of the metal cutting machine tools in their own factory were made in-house. The machine tools they build are computer-controlled, and often run unattended, so their production line is substantially self-operating.
- Assembly is one of the steps in production. An example of partial self-assembly is the International Space Station, where a large robot arm was used to install additional parts of the Station. Some Tower Cranes are able to increase their own height, by using a jacking attachment to add new sections to their support tower.
3D Printing or Additive Manufacturing (AM)
- The general AM process is to add material in series to a part, under computer control. This is the reverse of machining with cutting tools, which removes material from starting stock to produce a part. Certain AM machines, such as the RepRap 3D Printer, are intentionally designed to print copies of their own parts, along with being able to make parts for other uses. Single 3D printers can't make parts from all the types of materials from which they are built, or make more complex parts like motors and electronics. So they are only partly self-replicating.
Related Projects
- Open Source Ecology - This is an ongoing project to develop a "Global Village Construction Set", a set of 50 machines which together are intended to produce most of their own components and support most human needs. Besides the machines, you would need enough farmland and labor to operate them. It is an example of an intentionally designed starter set, with machines designed for easy fabrication. The project is notable for building and testing actual hardware, in some cases multiple versions and copies. Criticisms of the project include a "shotgun" design approach, without justifying why these 50 are the right set to build, which order they should be built, or what sizes are required. Another criticism is a static level of automation rather than starting simpler and upgrading. The included machines still require a lot of labor to operate. The project appears to be making slow progress after an initial burst of efforts in 2011-13.
- NASA In-Situ Resource Utilization (ISRU) - The 2010 NASA Technology Roadmap identified using local materials and energy as an important technology area for future space missions. The ISRU category, Technology Area 7.1 (section 2.2.1 of the roadmap document) includes mining and production tasks, and mentions self-replication and maintenance. These are similar ideas to what Seed Factories encompass. As of the 2017 Budget Estimate, NASA is devoting a small part of their Space Technology program funds to advanced manufacturing and ISRU, at a concept level and some experimental testing. The work is divided among several NASA centers (Ames, Marshall, and Kennedy). NASA in general focuses on individual technology elements, and lacks a strong systems analysis approach. Therefore it underestimates the leverage this technology has on their overall programs, and inadequately funds it relative to areas like launch vehicles and propulsion. They also do not consider Earth applications of the technology, because terrestrial manufacturing is not part of the agency's mission.
3.0 - The Seed Factory Project
These books are being developed as part of the Seed Factory Project, which is entirely devoted to research and testing of self-expanding and self-improving type systems. The books and the project's other work is far from complete. Here we provide a short description of the history and progress of the project. We welcome communication with and contributions to our work from others, including to these books. We can be can be reached through the contacts listed at the end of the Preface page.
3.1 - Background and Origin
In 2012 a conceptual design study for a program of Human Expansion beyond Earth was started, as part of a textbook on Space Systems Engineering. That study has since been extended and makes up Part 4 of the book, and the book is now volume II of this set. Self-expanding production was identified as a key technology in making large space projects affordable. Producing fuel, other supplies, and hardware from local materials greatly reduces the mass and cost of what needs to come from Earth. Subsequently this author (Eder) realized that the same technology also has value on Earth. It can be used to make products unrelated to space projects, as well as building space hardware and the transport equipment to get it to space. Experience gained with such manufacturing systems on Earth can then be applied to future space projects.
The needs on Earth are more immediate and currently much larger scale than in space. So by early 2013 the study work had shifted to designing Earth versions of Seed Factories first. The operating environments, material and energy sources, and difficulty of delivering equipment is quite different here. This leads to different designs and growth paths. The idea of self-improving/expanding/evolving/upgrading systems also seemed important in an era of smart tools. We therefore started a second book (this one) for general coverage of self-production and seed factories and their use on Earth. The two books are now a two volume set, with volume II covering the very different circumstances in space. They are not only connected by applying the same concepts, but by the fact that the first self-improving systems made for use in space would necessarily be built on Earth.
Theoretical development of new ideas, like the ones in our studies, is a necessary first step. But their real value comes from putting them to practical use. So we started the Seed Factory Project to go beyond ideas, to developing and building physical prototypes to prove out the technology. The Project is intended as an open source collaboration. Anyone with relevant skills is invited to contribute to the design work. Specific products or physical fsystems built with the technology would be privately owned. If good results are obtained from the prototypes, then the next step would be building full working factories. Experience gained would be incorporated back into updates for the books.
3.2 - Work in 2013-2016
The work during 2013 focused on a single design for a sustainable community of several hundred people. They would meet 85% of their physical needs from a matured Community Factory and the products it makes. The remainder would be met from outside sources. 85% was seen as a reasonable goal for a first generation design. The design study is archived in Section 2.3.2.9 A of the Project workbook, and notes in section 9.0 of this book.
From the results of that study we identified four different design examples, with different end points once matured. The first of these, Personal Production, is related to the original study, but focused more on the early stages and how to bootstrap getting started. It is described in Section 5 of this book. The other three are the Makernet (Section 6), which is a distributed production network in multiple locations; Industrial Production (Section 7), which looks at starter sets that grow to large-scale production; and Remote and Difficult Locations (Section 8), which looks at bootstrapping and starter sets for regions that are far from developed areas, less hospitable, or both. All four examples are currently incomplete. By doing several different designs, we hope to evolve general design principles and methods. It should also indicate how differing end goals affect the starter set, and what areas need more research and technical improvement.
Besides specific design examples, we also started working on general design tools. One of these is a resource model and flow network. This traces inputs and outputs from outside sources, among the various factory elements, and to the end users for the products. This makes sure all resources are accounted for, and the factory equipment is properly sized. By treating the mature factory as part of the product outputs, you can then recursively work back to find a starter set that leads to the chosen end point. We expect to use conventional design and engineering methods along with any new ones like resource models that we develop in the project.
2014 was consumed by funding, locating, purchasing, and starting to set up an R&D site in the southwest Atlanta area. The property includes almost 3 acres and some existing buildings, which was enough to start working with. If the project outgrows that space, there are many industrial buildings and parcels of undeveloped land in the area. 2015 went largely to project planning, high level systems engineering, setting up an office, and organizing project technical files. Since then there has been an ongoing effort to build a technical reference library, so that people besides ourselves can gain the knowledge and skills to start their own projects.
The Seed Factory idea was originally proposed to make large-scale space projects feasible, and that is still an eventual goal. The high level systems work led to a report on extending civilization beyond Earth, using it as a key technology. An important result of that work was identifying a logical sequence of project phases starting with home/hobby scale production. Each phase can produce equipment for the next phase, leading to expansion throughout the Solar System and beyond if taken far enough. In 2016 we started incorporating that plan back into the two Wikibooks, with the earlier phases described in this book, and the later space-related ones in volume II.
3.3 - 2017 to Date
We continue to develop the two online books, and the related project data which can mostly be found in the above linked project workbook. In parallel we are continuing to develop our R&D site, planning a start-up production cooperative as a first project, building a technical team, and working with other groups and projects. We had begun working with local area makerspaces, who already have well-developed workshops, but the COVID-19 pandemic and economic recession temporarily stopped outside activities.
4.0 - Questions and Planning
Self-improvement is not new. Ecosystems, civilizations, and people in the course of their lives have long improved themselves. However, purposely designing technical systems for self-improvement is a relatively new idea, and mostly untried as a way to organize production. So there are unanswered questions about how to design, build, and operate them. We gather some of these questions here to spur thought and further work. Other questions and subjects that need work are found across both books and our project notes.
One way to address these questions is developing an R&D plan for our project, which we make a start at below. But the unknowns are greater than we can reasonably expect to cover in a small project or pair of books and supporting data. A seed factory is a complex design involving multiple engineering fields. So we invite others to take up the challenge. We hope that with your knowledge, experience, and creativity we move the concepts forward into the realm of practical application.
4.1 - Open Questions
Feasibility
- Is existing technology sufficient to meet the desired goals for self-expansion, recycling, and automation?
- -- If not, what new technology or improvements are needed?
Design
- What should be in a particular starter set, and in what order should new equipment be added?
- -- How does the starter set and growth path depend on the scale and type of products of the mature system?
- -- How does the starter set and growth path depend on the resources and environment at a particular location?
- -- When is it better to use general purpose equipment with attachments vs. more specialized and dedicated units?
Growth
- What is the optimal path to increasing the percentage of self-production (closure) and automation?
- What is the fastest way to grow total factory capacity?
- What is the relationship among starter set complexity, physical scale, initial cost, and growth rates?
Economic & Social Questions
- In purely financial terms, how do self-expanding systems compare to conventional factories for capital and production costs?
- Does the seed factory approach better meet people's material and other needs than conventional specialized factories?
- How should production capacity be divided between internal maintenance and growth, outputs for the owners, and products for sale?
- What are the social effects of self-ownership, acquiring new skills, and reduced need for conventional jobs?
- How can projects be organized to avoid worsening economic inequalities?
4.2 - R&D Planning
A lot of work needed to answer the above questions, and bring finished designs and working examples of self-improving technical systems into existence. This kind of work is generally called Research and Development (R&D), and must logically come before later stages in a system's life-cycle, such as fabrication and operation. The design of a self-improving system can be quite complex, so we adopt Systems Engineering methods, which were developed to handle such complex systems over their full life-cycle. This includes the R&D portion of the work.
The combination of concepts and features for self-improving systems, which were noted in heading 1.0 above, is new. But many of the elements which would make up such systems, such as the production processes used, are not, and have extensive history. The ones which are new must first be explored, selected, and tested. Taking a new technology from bare ideas to being ready for widespread use is part of the R&D process. Where a technology stands in that process can be measured on a Technology Readiness Level scale. It needs to reach a sufficient level of readiness before being incorporated into operational systems. Further work is then required to combine existing and new elements into a coherent system, a process known as System Integration. Work is also needed to prove the potential advantages of self-improvement are in fact real, by how much, and under what circumstances. Early steps towards proof include preliminary designs, mathematical models, and simulations. Those are followed by building prototypes and testing them, a process called System Validation.
As a start towards the R&D work, we can identify the current state of knowledge and experience in the fields identified in 2.0 above. We can also look at what progress is being made in related projects and technology. By comparing existing knowledge and current work to what is needed for our proposed systems, we can start to develop plans to fill in the gaps. We don't know everything we don't know at the start. Additional R&D needs will emerge in the course of concept exploration, design, and even later stages of testing and operation. For example, we may find deficiencies in testing a prototype, which requires further improvement in a given technology. So at this point we can only make a start at at R&D planning, and expect the plans to evolve on a continuing basis.
4.3 - R&D Process and Identified Tasks
Even though our understanding of self-improving systems is incomplete, we think we know enough to start the research and developing designs for particular purposes. We can follow a similar R&D Process for each system application, reusing particular technologies and designs where possible. The work can be divided into general R&D that applies across different systems, and tasks that are particular to specific applications and examples. The following task list includes what we have identified so far. It is preliminary, and will need extensive revision as more people work on the concepts, develop new ideas, and gain a better understanding of what needs to be done:
4.3.1 - General R&D Tasks:
- (1) Continue Conceptual Work
This includes the following component tasks:
- Identifying key parameters and formulas for self-expanding integrated systems, so that they can be modeled and optimized.
- Comparing the state of the art in automation, robotics, software, AI, and other related fields to what is needed in this type of factory. This either establishes feasibility or defines areas for further research and development.
- Collecting designs and concepts developed by others outside this project, to see if they apply or can be adapted for use.
- Refine example applications in more detail to incorporate the self-expansion and other concepts identified above, verify they are feasible, and estimate their cost and economics.
- (2) Component Research
Where new or modified technology is identified as necessary, this task covers developing the technology. It includes theoretical concepts, analytical design, and laboratory and component level testing. Once sufficiently well tested, the technology can then be added to the available portfolio for detail design and prototyping of full syestem elements. Component level work can be done at any location as an open source collaboration.
- (3) Continuing Work
After an initial set of prototypes are developed, they can be spun off into a working factory project for owner-operators. Such a factory would demonstrate the complete system works as intended and satisfies the original design goals. Feedback from actual use would help in designing improvements and upgrades, and later generation versions.
The R&D work would continue in parallel with operational use, for several reasons. First, it is not likely an ideal design will be developed on the first try. Second, other locations and products besides the original ones will likely require modified designs and more testing. Third, technology in general does not stand still. Last, an initial set of hardware will not cover all the kinds of equipment that may be wanted. Continuing work would develop upgrades and new designs and feed them to factory projects when they are ready. Prototypes for different kinds of locations would either be built at those locations, or built at an existing facility and then delivered. Using the original set of prototypes to help build the later equipment can demonstrate the expansion capacity of the designs.
4.3.2 - R&D for R&D Locations
The places where the R&D work is carried out also need to be designed. This includes offices, laboratories, production areas for prototypes, and test sites. In some cases existing facilities and equipment can be used, but in other cases they will need modification, or unique designs will be needed, such as for a special test chamber. Specific needs for this heading are still to be determined.
- Build Conventional Workshop - This is for fabrication of custom prototype elements. Where it makes more sense, these elements can be produced elsewhere, then delivered and assembled.
- Build Prototype Test Area - Once prototypes are assembled, they must be tested through operation. This requires a suitable place to do the testing, whether indoors or outdoors.
4.3.3 - R&D for Personal Production
This includes work specific to the first design example: Personal Production.
- (1) Preliminary Design
This step takes the concept-level designs to sized and configured elements which are ready for final drawing preparation. For example, for a machine tool in the factory, a preliminary design level would specify the dimensions of the major parts, power level, accuracy, and provide layout drawings. For software, a preliminary design identifies the major functions, inputs, and outputs, and how they relate to each other.
- (2) Build Prototypes
This includes designing prototype elements, setting up production and test areas for them, and the actual manufacture and test of the prototypes. Small scale prototypes of the factory elements can be built at distributed locations. Eventually large scale prototypes or linking multiple factory processes into a complete system will require a dedicated fixed location. This is especially true of collecting renewable energy and growing organic materials, which requires significant land area. The project may work with other R&D institutions, non-profits, etc. which already have facilities, if that makes progress easier. Whatever knowledge and experience gained in the project would then be distributed for the benefit of people in general. More detailed steps include:
- Design Prototype Hardware
- Design Prototype Software
- Fabricate and Assemble Prototype Hardware
- Test Prototypes
4.3.4 - R&D for the MakerNet
This includes work specific to the second design example.
4.3.5 - R&D for Industrial Production
4.3.6 - R&D for Remote and Difficult Locations
[Merge or Move]
Machines in general involve movement, but in the past the type of movement was fixed by design. Robots are machines which can perform movement under automated or remote control, where the specific movements are not predetermined. You can change the task a robot performs by changing the control inputs. Robotics has developed in parallel with more fixed types of automation. By now (2017) automation and robotics are extensively used in manufacturing, and are starting to be used in other environments. In the past, people have used tools and machines to make more tools and machines. The development of smart tools means the machines are becoming more able to do so on their own, without needing people to do much of the work.
Self-expanding production systems which bootstrap from seed factory-type starter sets are a new way to organize production. You cannot yet buy such starter sets or obtain plans and instructions for them, and working examples do not yet exist. Therefore Research and Development (R&D) is needed to bring such systems into existence. While complete systems like these do not yet exist, much of the knowledge required, and component elements do. This section reviews the existing knowledge and experience available, what related work is already in progress, their status and unanswered questions, and makes a start at planning further R&D work that is needed. We are at an early stage of the R&D work, so this section should be considered preliminary and incomplete.